How an IoT-based liquid tank level monitoring system works?
What is liquid level monitoring system?
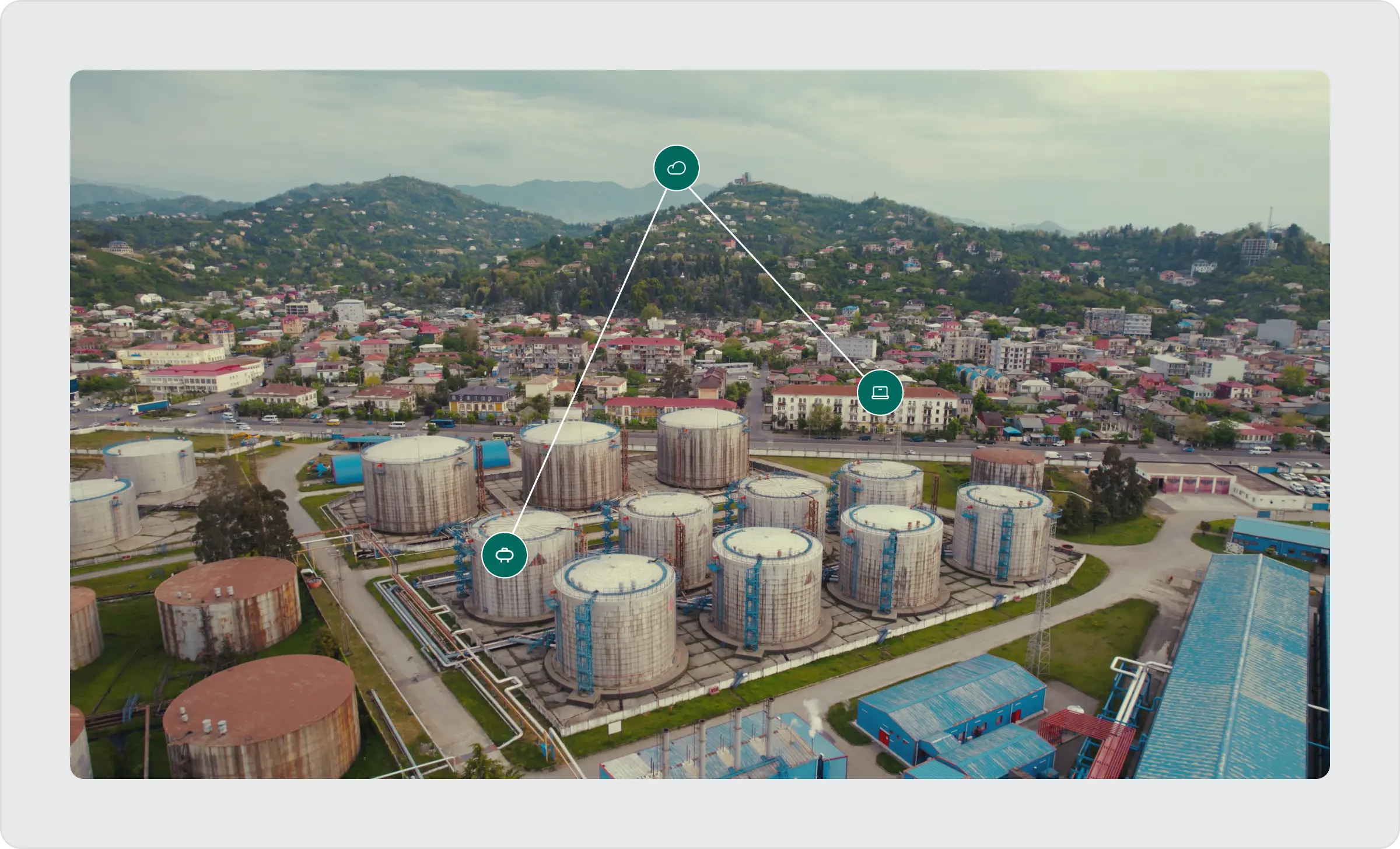
A liquid level monitoring system is a solution designed to monitor and control the amount of liquid in one or more tanks. This solution involves the use of three essential components:
- Sensors to accurately detect the liquid level;
- The communication layer to transmit the data from sensors to the platform;
- Platforms to store, process, and display the data.
Accurate liquid monitor level in a tank is critical to a wide range of industries, including water treatment, chemical manufacturing, food and beverage, oil and gas, and many others that require precise control of liquid volumes for operational efficiency, safety, and regulatory compliance.
The general goal of the tank level monitoring system is to provide real-time data on the amount of liquid stored, enabling efficient management of liquid resources. It can predict potential overfilling or depletion of critical stocks by creating automatic alerts when liquid levels are expected to be too high or too low. Tank fluid level monitoring systems not only ensure operational continuity and safety but also provide valuable data on fluid conditions, such as temperature and pressure. This information helps optimize resource use, improve environmental sustainability, and reduce storage and supply chain costs.
How Liquid level monitoring system works?
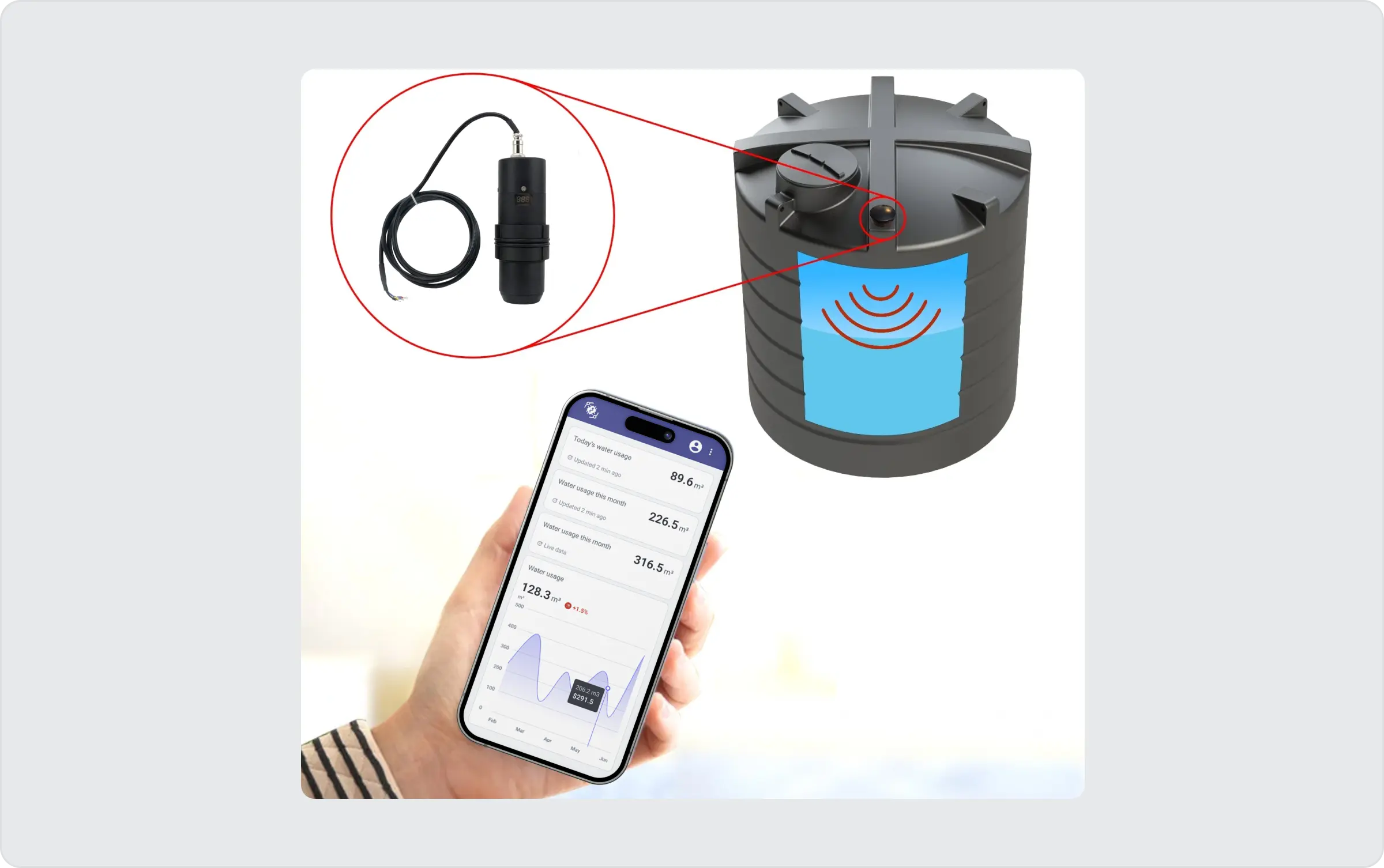
Measurement can be carried out using a variety of IoT-powered liquid level monitoring sensors such as ultrasonic sensors, radar level sensors, float switches, and pressure sensors, which can measure liquid levels without direct contact with the liquid or by direct immersion in the tank or reservoir. Each of these sensors has its own advantages and is selected based on installation conditions, the geometry of the storage tank, and the construction material of the tank. Usually, the sensor is mounted on the lid of a closed tank or suspended by a rod or rope over an open tank.
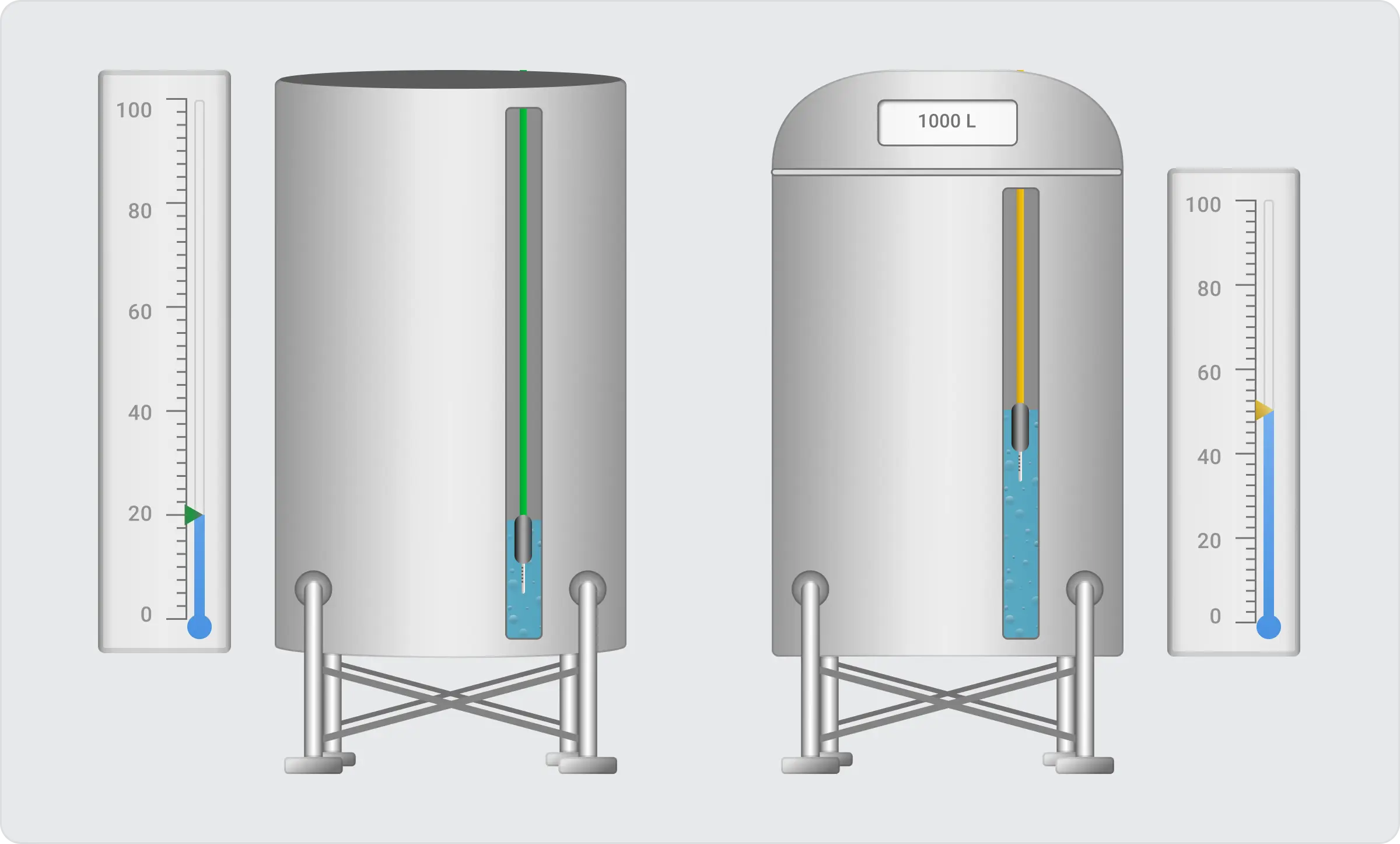
Once installed, the sensor can check the amount of liquid in the tank. They operate by emitting signals—sound waves for ultrasonic sensors or electromagnetic waves for radar sensors—towards the liquid surface and measuring the time it takes for these signals to bounce back. This method helps calculate the fluid level within the tank.
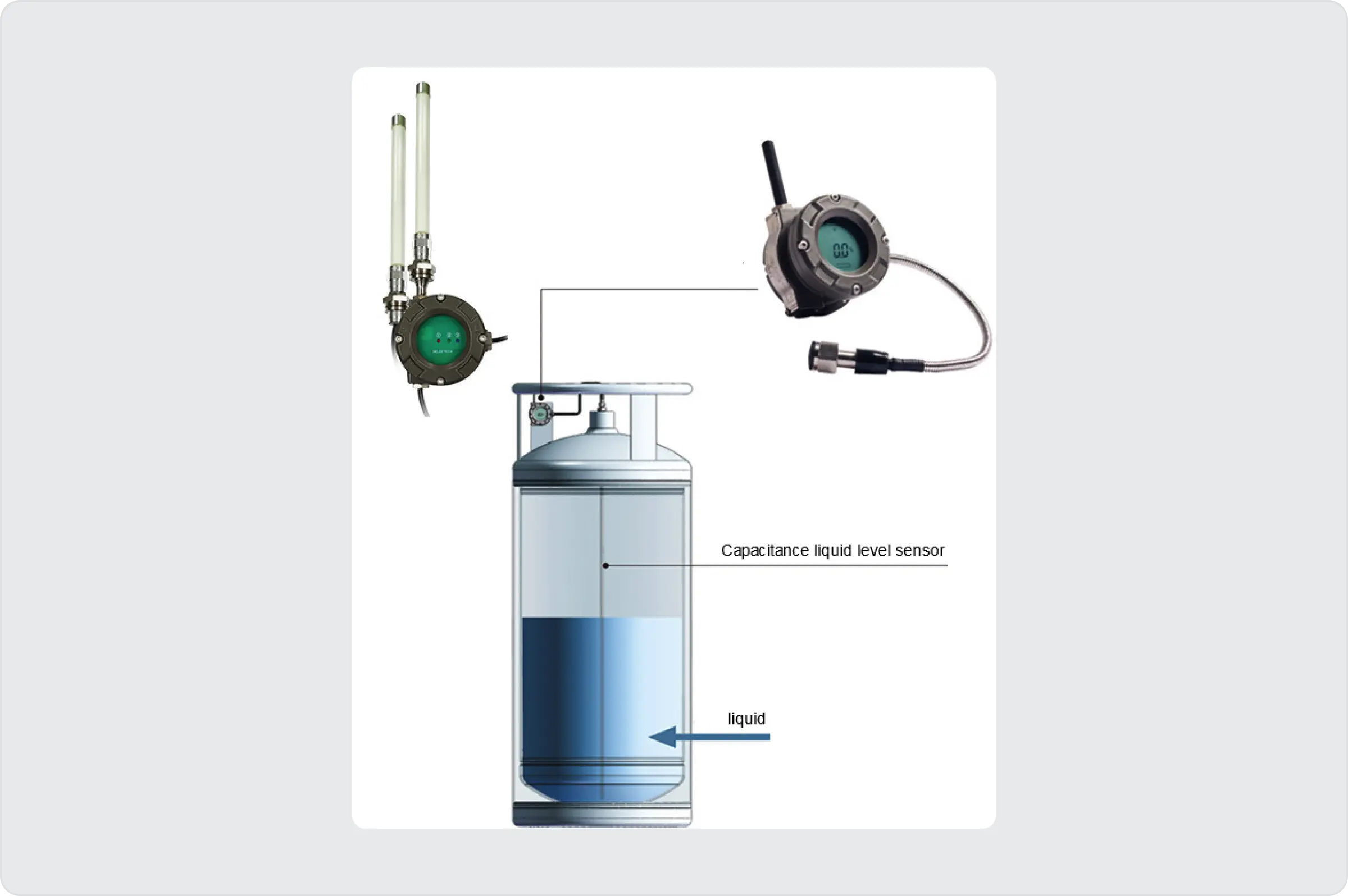
Sensors or local data loggers transmit measurements to a central monitoring system (IoT Platform) using communication technologies such as LoraWAN, Sigfox, or NB-IoT. These technologies facilitate efficient long-range communication with low power consumption, enabling remote monitoring of the level of liquid indoors and outdoors.
ThingsBoard IoT platform in the tank level monitoring system
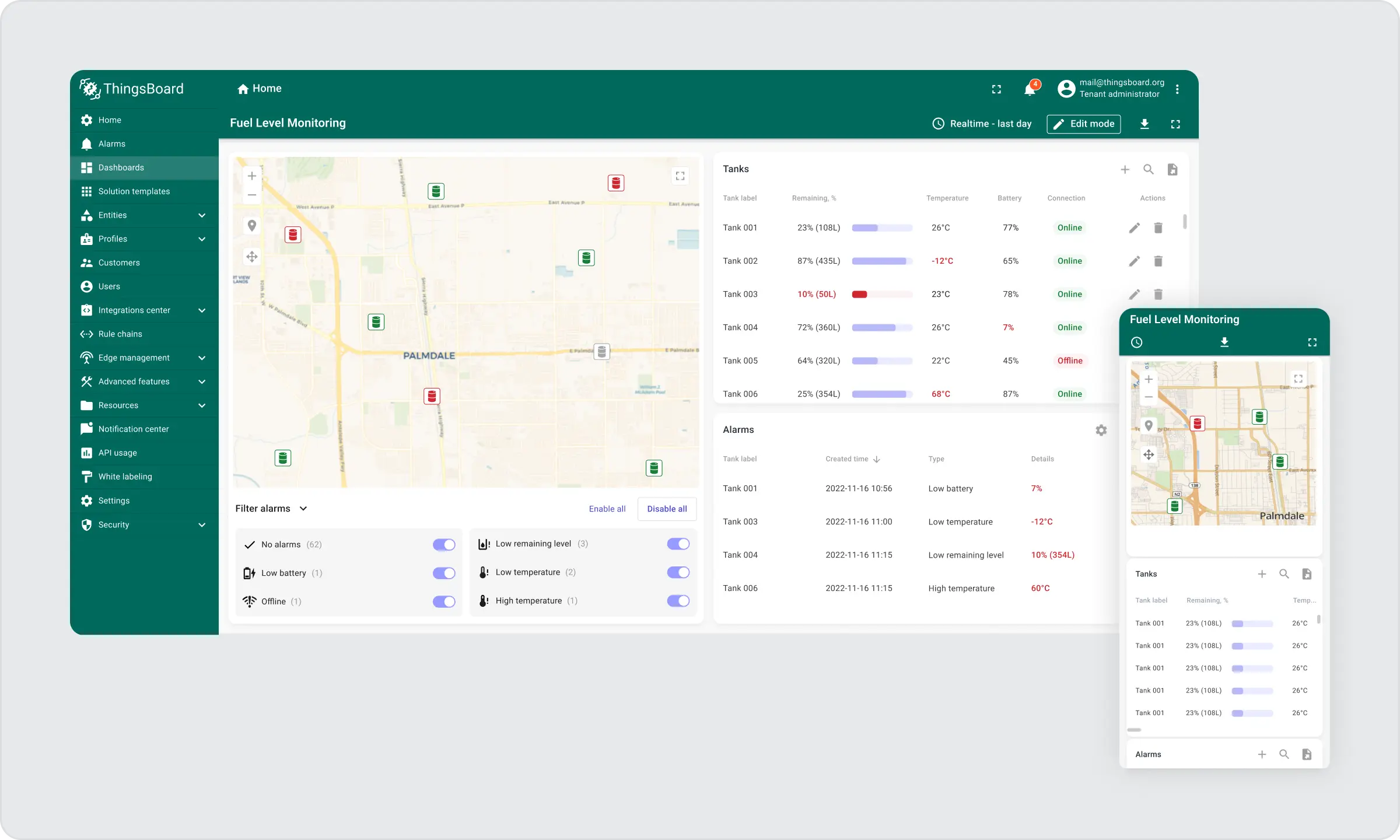
Using an IoT ThingsBoard platform to monitor the levels of liquids in tanks brings a lot of benefits. It makes it possible to get accurate, real-time information and manage it effectively, ensuring operations run smoothly and safely. With features like user management, device compatibility, and customizable options, the ThingsBoard platform is a versatile and powerful tool for any business that deals with liquid storage and management.
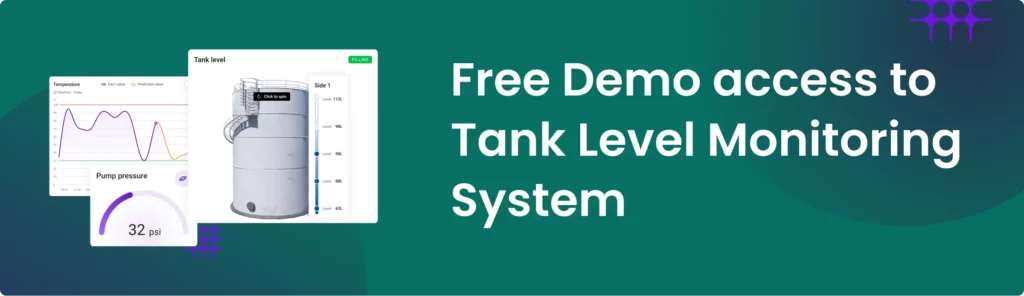
Explore capabilities one of the best IoT Visualization Platform
GET ACCESSThe main features of ThingsBoard can help unlock the full potential and be sure that all the capabilities of modern IoT systems are used:
- Telemetry Data Collection: Collect and store telemetry data in a reliable way, surviving network and hardware failures. Access collected data using customizable web dashboards or server-side APIs.
- Device Management: Provides the ability to register and manage multiple devices. As part of the ThingsBoard Tank Level Monitoring System, you can connect various devices to measure liquid level, pressure, and temperature. Using multiple Devices for the remote reading of liquid tank contents helps to measure not only level but also temperature, which is important for certain types of liquids, as changes in temperature can affect volume and viscosity.
- Alarms Management: Provides the ability to create and manage alarms related to your entities: devices, assets, customers, etc. Allows real-time alarm monitoring and alarm propagation to related entities’ hierarchy. Raise alarms on device disconnect or inactivity events.
- Multi-tenancy. Support multi-tenant installations out of the box. Single tenants may have multiple tenant administrators and millions of devices and customers.
- Data Visualization: Provides 30+ configurable widgets out-of-the-box and the ability to create your IoT visualization platform using a built-in editor. Built-in line charts, digital and analog gauges, maps, etc.
- Horizontal scalability. The amount of supported server-side requests and devices increases linearly as new ThingsBoard servers are added in clustering mode. No downtime, server restarts, or application errors.
- Customization and Integration: Extend default platform functionality using customizable rule chains, widgets, and transport implementations. In addition to MQTT, CoAP, and HTTP support, ThingsBoard users can use their own transport implementations or customize the behavior of existing protocols.
ThingsBoard Tank Level Monitoring Solution offers real-time insight into liquid levels, facilitating proactive management of liquid stocks and refining operational workflows. The solution employs advanced technology, including adaptable sensors and robust communication protocols, to track tank fluid levels accurately. With an intuitive dashboard, users can effortlessly monitor tank state, configure measurement details and custom alerts, and track liquid consumption. Mastering liquid management processes can diminish operational disruptions and ensure continuous fuel availability, leading to streamlined operations and enhanced customer satisfaction.
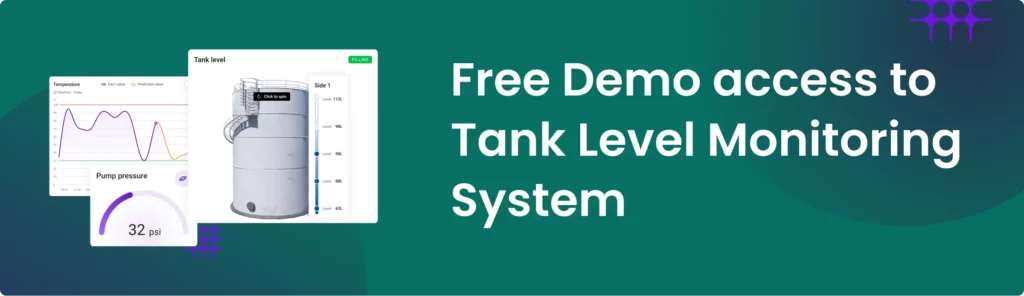
Explore capabilities one of the best IoT Visualization Platform
GET ACCESSPractical Uses Сases of liquid tank level monitoring system
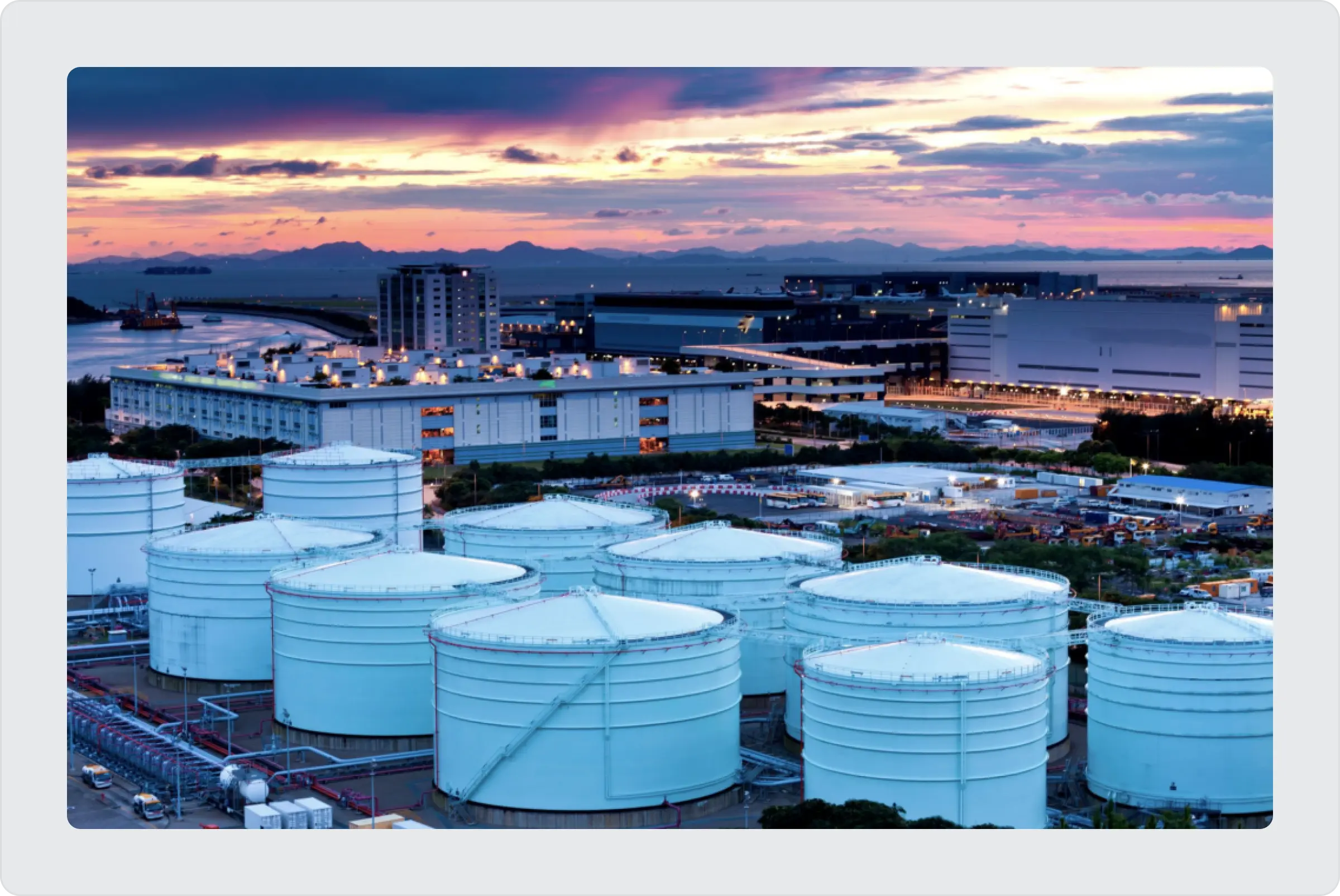
Oil & Energy Industry
In the oil and energy industry, liquid-level monitoring systems are not just a tool for measurement; they are an integral part of operational strategy, safety management, and regulatory compliance. With the advent of advanced IoT technologies, these systems provide more than just data—they enable smarter decision-making, enhance operational efficiencies, and help safeguard both the environment and the public.
Here are a few examples of remote tank level monitoring for Oil & Energy in action:
- Hauling companies use smart tank sensors during custody transfers to track how much oil or water they pull from central tank batteries;
- Oil and gas operators use tank level monitors to monitor chemical inventory and usage related to promoting asset integrity or maintaining flow assurance;
- Commercial businesses use tank-level monitors to measure diesel consumption rates for backup generators or automate stock-out notifications for underground gasoline storage tanks.
Water & Wastewater Industry
Liquid level monitoring systems are necessary for the water and wastewater industry, enhancing operational efficiency, ensuring environmental compliance, and protecting public health. These systems provide critical real-time data and control capabilities that allow for the effective management of water resources and treatment processes in an increasingly complex and regulated environment.
Here are a few examples of remote tank level monitoring for wastewater treatment in action:
- Treatment plant operators use tank level sensors to monitor separation in quiescent basins and track disinfecting chemical supply;
- Saltwater disposal facilities use tank monitoring to track liquid volumes for disposed and injected wastewater and prevent overflows in storage tanks;
- Waste management companies rely on smart tank sensors to collect data about methanol usage rates for leachate treatments and prevent leaks or spills in clarifier tanks.
Agriculture Industry
Agriculture’s strategic use of liquid level monitoring systems transforms how water resources are managed, promoting more sustainable and efficient practices. Whether through enhancing irrigation practices, supporting livestock, optimizing aquaculture operations, or managing scarce water supplies, these systems play a crucial role in modern agricultural operations, aiding farmers in navigating the challenges of today’s agricultural landscape.
Here are a few examples of remote tank monitoring for agriculture in action:
- Agriculture companies use tank monitors to track treatment rates for chemigation;
- Operators depend on smart tank level sensors to monitor fertilizer and additives inventory for irrigation processes;
- Sustainable agriculture farmers use tank monitoring to track rainwater collection and ensure livestock have enough to drink.
Food & Beverage Industry
In the food and beverage industry, liquid level monitoring systems play a important role in enhancing operational efficiency, ensuring product quality, and maintaining regulatory compliance. These systems enable better management of ingredients, improve production processes, and ensure thorough sanitation, making them invaluable tools for any food and beverage production facility.
Here are a few examples of remote tank monitoring for Food & Beverage Industry in action:
- Food and beverage producers use tank level monitors to monitor market-ready output of beverages;
- Manufacturers use tank sensors to track the usage of additives, like dyes and emulsifiers, used in many food production processes.
Chemicals Industry
Liquid level monitoring systems are critical in the chemicals industry, addressing a range of critical functions from safety and compliance to efficiency and quality control. By leveraging these systems, chemical companies can enhance their operational capabilities, mitigate risks, and maintain a competitive edge in a demanding market environment.
Here are a few examples of remote tank monitoring for Chemicals Industry in action:
- Chemical manufacturers use tank level monitors to track distributed chemical inventories across large geographic footprints
- Operators use smart tank sensors to identify where their chemicals are and when stock-outs are pending
- Chemical companies use tank level monitoring to streamline inventory and supply chain management
Conclusion
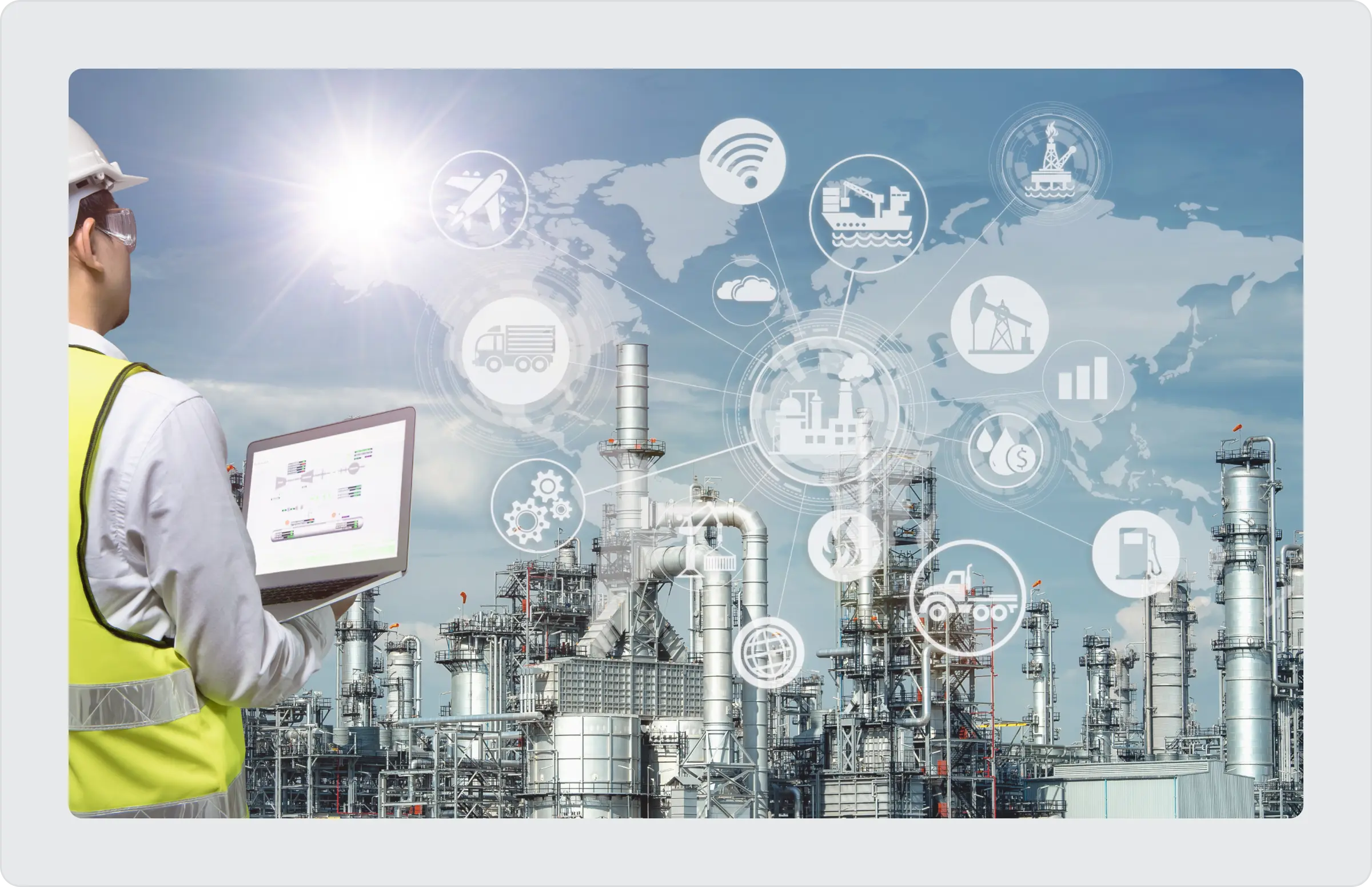
Liquid level monitoring systems are more than just tools for measuring liquid levels. They are integral components of a strategic approach to modern industrial operations. They combine technology, safety, and environmental protection, giving industry the capabilities it needs to meet today’s challenges. By implementing these systems, industries can achieve greater operational efficiency, improve safety protocols, ensure compliance with strict standards, protect the environment and ultimately promote sustainability.